Bob,
I am considering a project similar to your lost plastic Milwaukee Road Erie. As I recall, you mentioned that you screw the resultant castings (cab and body) together. I presume you glue plastic "blocks" in position so that they will align when the two post burnout metal sections are set to be joined.
Does it matter what type plastic the "blocks" are made from? Do they need to be the same material as the loco shells? I presume a glue like Tenax is suitable to glue the blocks to the Loco sections.
I would appreciate any tips.
Thanks,
Rich
Soldering Sand Cast Doorstops
Soldering Sand Cast Doorstops
Last edited by E7 on Sat Dec 11, 2021 11:58 am, edited 1 time in total.
-
- Posts: 12858
- Joined: Sat Jan 13, 2007 7:57 pm
Re: Bob Turner
No - I do it with 1/4" square brass rod. I suppose you could do it with plastic - the problem is that sometimes the brass cools differently when going from thin to thick, and you may wind up with blemishes that are more difficult to hide than screw heads.
In either case, a successful lost-plastic casting is done with a "double burnout" - you double the time period the investment is in the furnace, to make sure all the ash is gone. Jay C does a lot of this, and helped me with the nose. The sides were sand-cast, and the foundry did a superb job. But they do not answer my e-mails, and my E7 sides have probably been lost.
I can do a discussion on how I hold the PA body together for soldering if you want. Change the title to "Soldering sand-cast doorstops" or something and I will go into a bit more detail.
In either case, a successful lost-plastic casting is done with a "double burnout" - you double the time period the investment is in the furnace, to make sure all the ash is gone. Jay C does a lot of this, and helped me with the nose. The sides were sand-cast, and the foundry did a superb job. But they do not answer my e-mails, and my E7 sides have probably been lost.
I can do a discussion on how I hold the PA body together for soldering if you want. Change the title to "Soldering sand-cast doorstops" or something and I will go into a bit more detail.
Re: Soldering Sand Cast Doorstops
Note: My Loco will not have any doorstop parts....will be burning out the whole engine,
Jay mentioned the vessel (can't recall the proper name of the thing) that holds the plastic part and sand for the burnout could not contain a complete Loco, so the Loco must be cut into 2 pieces. If I could find a foundry that could do the whole thing, that would be the way I'd go, and that would eliminate the "joining" issue.
I thought I could glue rectangular solids inside onto the sides and inner roof of the nose, and put mates to match up inside the body. Then drill and screw them after the thing was cast.
Sounds as though that might be problematic because of the thickness of the plastic blocks. Maybe the only way to go is to solder pieces on after the castings are done? The joint lines would be easy to fill after the thing was screwed together.
Way back I spoke with Bob Stevenson, and he said he could have a plastic engine fired. Don't know what foundry....maybe the same? Do you do the tabs to mount the body to the chassis, or are they soldered on after the fact?
Rich
Jay mentioned the vessel (can't recall the proper name of the thing) that holds the plastic part and sand for the burnout could not contain a complete Loco, so the Loco must be cut into 2 pieces. If I could find a foundry that could do the whole thing, that would be the way I'd go, and that would eliminate the "joining" issue.
I thought I could glue rectangular solids inside onto the sides and inner roof of the nose, and put mates to match up inside the body. Then drill and screw them after the thing was cast.
Sounds as though that might be problematic because of the thickness of the plastic blocks. Maybe the only way to go is to solder pieces on after the castings are done? The joint lines would be easy to fill after the thing was screwed together.
Way back I spoke with Bob Stevenson, and he said he could have a plastic engine fired. Don't know what foundry....maybe the same? Do you do the tabs to mount the body to the chassis, or are they soldered on after the fact?
Rich
-
- Posts: 12858
- Joined: Sat Jan 13, 2007 7:57 pm
Re: Soldering Sand Cast Doorstops
I do not have assembly photos - I will take some if I assemble another sand cast doorstop Diesel.
First thing I do after smoothing and cleaning the castings for a good fit is to add the truck mount rails, which serve as alignment bars for the nose castings. I clean them and mark - they probably would not interchange. Mine are usually 1/8" above the lower belt line, leaving room for a thick Bakelite bolster.
I fasten them with 2-56 brass screws - lately the heads of the screws are inside the body, so all I have to do outside is trim the threaded part that protrudes outside the body.
A two- piece nose should be soldered snd bolted together separately. Bolts are not really necessary, but they maintain alignment if the nose solder liquifies during the body soldering effort.
Holding the roof in place is semi-tricky. I use aluminum spacers bolted to the sides through portholes or windows with steel screws, and then I drill them for screws that go into the roof, clamping it against the tops of the sides.
If the back end is not securely captured, I pin it with .032 brass rod. Doesn't take much to hold it.
Finally, I use giant C clamps to make sure roof and sides stay aligned, and to space the body off the firebricks while heating.
Mapp gas and a pencil torch tip are used to heat to solder temperature. I use a liquid acid flux, applied liberally on all joints, and 60-40 rosin core (easier to buy; rosin is useless but not in the way). Put a few chips on seams so you can see when it is hot enough to flow, then hit the joint with the unrolled solder. Wear a glove, and don't touch the casting except with pliers.
First thing I do after smoothing and cleaning the castings for a good fit is to add the truck mount rails, which serve as alignment bars for the nose castings. I clean them and mark - they probably would not interchange. Mine are usually 1/8" above the lower belt line, leaving room for a thick Bakelite bolster.
I fasten them with 2-56 brass screws - lately the heads of the screws are inside the body, so all I have to do outside is trim the threaded part that protrudes outside the body.
A two- piece nose should be soldered snd bolted together separately. Bolts are not really necessary, but they maintain alignment if the nose solder liquifies during the body soldering effort.
Holding the roof in place is semi-tricky. I use aluminum spacers bolted to the sides through portholes or windows with steel screws, and then I drill them for screws that go into the roof, clamping it against the tops of the sides.
If the back end is not securely captured, I pin it with .032 brass rod. Doesn't take much to hold it.
Finally, I use giant C clamps to make sure roof and sides stay aligned, and to space the body off the firebricks while heating.
Mapp gas and a pencil torch tip are used to heat to solder temperature. I use a liquid acid flux, applied liberally on all joints, and 60-40 rosin core (easier to buy; rosin is useless but not in the way). Put a few chips on seams so you can see when it is hot enough to flow, then hit the joint with the unrolled solder. Wear a glove, and don't touch the casting except with pliers.
-
- Posts: 12858
- Joined: Sat Jan 13, 2007 7:57 pm
Re: Soldering Sand Cast Doorstops
Our posts crossed.
I did one MTH PA in a single piece using a "shell cast" process. Had they done a double burnout it would have been perfect. They made several mistakes, but I got a usable model out of it.
Dennis did two PA bodies for me - yes, sawed in half. We may have added tabs, but better to do that afterward, since the interface may need cleaning up. Dennis is an expert - but first attempt warped badly. Might have not cooled sufficiently before removing the plaster.
There is 1/2% shrinkage. That means long grillework will not precisely fit.
Let me check on photos . . .
I did one MTH PA in a single piece using a "shell cast" process. Had they done a double burnout it would have been perfect. They made several mistakes, but I got a usable model out of it.
Dennis did two PA bodies for me - yes, sawed in half. We may have added tabs, but better to do that afterward, since the interface may need cleaning up. Dennis is an expert - but first attempt warped badly. Might have not cooled sufficiently before removing the plaster.
There is 1/2% shrinkage. That means long grillework will not precisely fit.
Let me check on photos . . .
-
- Posts: 12858
- Joined: Sat Jan 13, 2007 7:57 pm
Re: Soldering Sand Cast Doorstops
Here is the shell cast bronze PA. The technique is that thin layers of plaster are applied to the entire body inside and out, until they are thick enough to sustain the burnout and pour processes. This is different from the investment cast process, where the plaster is just poured over the wax or plastic parts.
The foundry did not burn it out adequately, so they inserted steel shot in the empty space to clean out the ash - and of course to mess up the fine detail of the MTH casting.
I should mention that I purchased the plastic bodies directly from MTH, and informing them of my nefarious purpose. All very legal.
Same with Atlas. Both were very nice about it - but then I am copying their artwork for a non-commercial purpose.

The foundry did not burn it out adequately, so they inserted steel shot in the empty space to clean out the ash - and of course to mess up the fine detail of the MTH casting.
I should mention that I purchased the plastic bodies directly from MTH, and informing them of my nefarious purpose. All very legal.
Same with Atlas. Both were very nice about it - but then I am copying their artwork for a non-commercial purpose.
-
- Posts: 12858
- Joined: Sat Jan 13, 2007 7:57 pm
Re: Soldering Sand Cast Doorstops
Here is the one Dennis did for me - nickel silver, and in two pieces. The joint is just ahead of the middle door, and I think we added a piece of styrene to make up for the shrinkage. As you can see, the detail was copied exactly.
The Santa Fe plated the sides of some of their Diesels with stainless, so I chose to simulate that with polished nickel silver. Not great - I think the Alclad II is a better idea for stainless.
Also, please do not be too judgey about those trucks - it was my first attempt at really scratchbuilding a complex sideframe master. If I ever have more made, I will put in fake springs and add the brake cylinders to the master before getting the mold made.
But no need - Lionel and others have made truly accurate sideframes for the PA - I believe you can still buy the kit from CLW, and that one was arguably the best ever done in O Scale (except maybe Key).
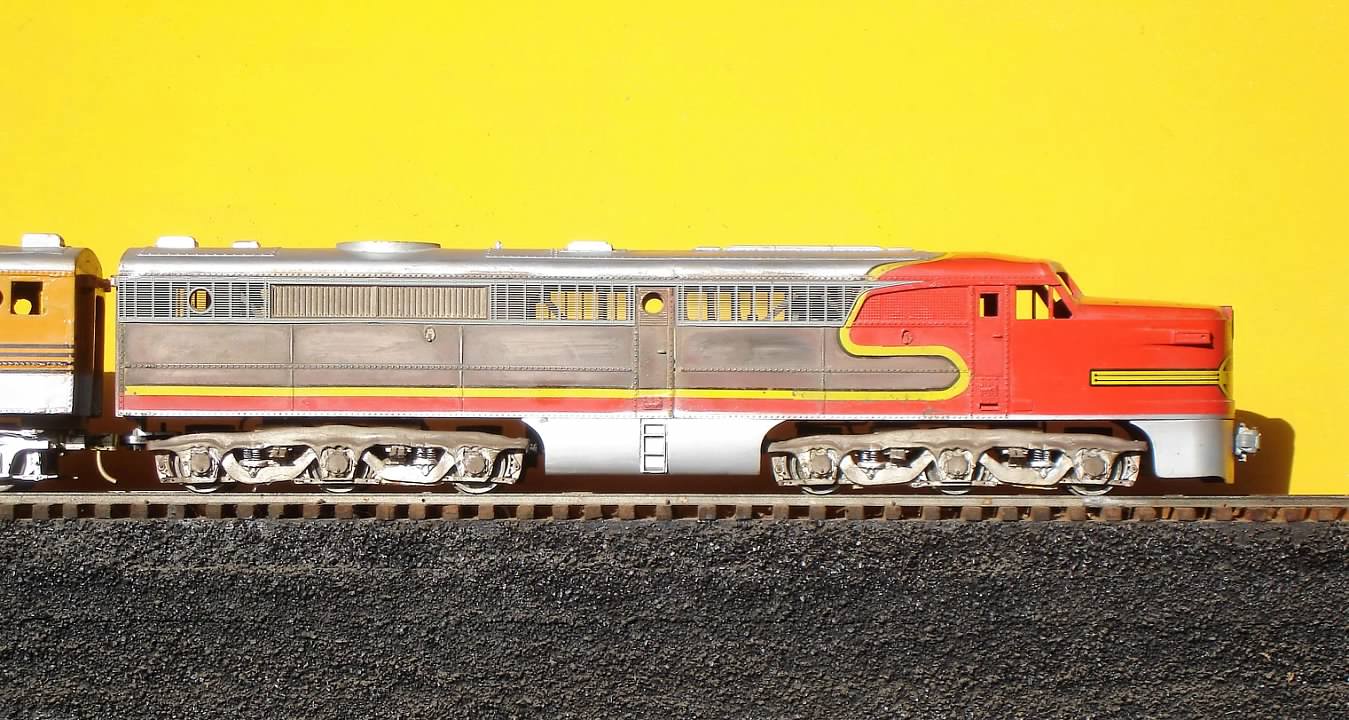
The Santa Fe plated the sides of some of their Diesels with stainless, so I chose to simulate that with polished nickel silver. Not great - I think the Alclad II is a better idea for stainless.
Also, please do not be too judgey about those trucks - it was my first attempt at really scratchbuilding a complex sideframe master. If I ever have more made, I will put in fake springs and add the brake cylinders to the master before getting the mold made.
But no need - Lionel and others have made truly accurate sideframes for the PA - I believe you can still buy the kit from CLW, and that one was arguably the best ever done in O Scale (except maybe Key).
Re: Soldering Sand Cast Doorstops
Bob, I didn't mean to mislead you, but the term "DOORSTOP" will NOT really enter into this project.
I want to burn out one of the old Rivarossi C-Liners and NO doorstop parts are necessary, since the complete bodies are easily available. The BIG question can it be done as one piece or two?
Then I hope to mount that piece or pieces to a more or less standard type chassis, where the body screws onto it.
The Rivarossi bodies are in my opinion, very accurate. The only thing that might need some work is the pilot.
My biggest question is if I have to go with two separate body sections, what is the best/easiest method to provide for screwing them together? That's why I was referring to putting "blocks" inside to drill and then screw the 2 pieces together.
typo
Rich
I want to burn out one of the old Rivarossi C-Liners and NO doorstop parts are necessary, since the complete bodies are easily available. The BIG question can it be done as one piece or two?
Then I hope to mount that piece or pieces to a more or less standard type chassis, where the body screws onto it.
The Rivarossi bodies are in my opinion, very accurate. The only thing that might need some work is the pilot.
My biggest question is if I have to go with two separate body sections, what is the best/easiest method to provide for screwing them together? That's why I was referring to putting "blocks" inside to drill and then screw the 2 pieces together.
typo
Rich
Last edited by E7 on Mon Dec 13, 2021 12:59 am, edited 1 time in total.
-
- Posts: 12858
- Joined: Sat Jan 13, 2007 7:57 pm
Re: Soldering Sand Cast Doorstops
"Doorstop" is a joke. We simply refer to very heavy models with less intricate detailing as doorstops, but we never use them to hold doors. The two Diesels above are exactly what you are doing.
I agree - the Rivarossi C Liner is an excellent candidate. The pilot is not that far off - fill with candle wax, then carve to your preferred shape. Long Island used that huge cardioid shape for coupler access.
I will look tomorrow to see if I used tabs in the pair that were done in two pieces - might try to find s "shell cast" foundry - they do things like trophies or animals.
I agree - the Rivarossi C Liner is an excellent candidate. The pilot is not that far off - fill with candle wax, then carve to your preferred shape. Long Island used that huge cardioid shape for coupler access.
I will look tomorrow to see if I used tabs in the pair that were done in two pieces - might try to find s "shell cast" foundry - they do things like trophies or animals.
Re: Soldering Sand Cast Doorstops
When I think "Doorstop", I think of the old sand cast pieces ala A&S.
Not exactly sure how i want to handle that pilot. The NYC had some with that smiley opening.
Not exactly sure how i want to handle that pilot. The NYC had some with that smiley opening.
Re: Soldering Sand Cast Doorstops
Rich
I agree the basic C-liner shell is a worthwhile subject, though one has to also watch the fan-count depending on the railroad modelled. Anyway, I'd think the best place to split that one would be just behind the cab doors.
I'd use three tabs sheared from thick brass strip as an alternative, one at the inside centre of the roof and one low on the inside of each side, drilled and tapped through some available flat area devoid of detail so they are easy to grind and blend afterwards.
Each screwed with brass 2-56 on both ends, you can loose them a little and adjust the relationships between the nose and the carbody until it's precisely where you want it. Doing the two sides first, up and down between the parts is a loosen-tighten deal, in and out a brass washer inserted under one or the other screw in a strip. Fore and aft is a loosen tighten deal too, but you have to decide if you want to fill the resulting gap or take it back apart and redress the joint (squaring on a piece of 3/8" plate glass with 320 wet-and-dry is a good way to go).
Once you have the two side strips tightened at your final alignment, then screw the strap in at the roof centre, adjust any tilt using the same methodology, and the whole is constrained/locked in place. Then you can crack out the torches and join the assembly.
Afterwards, you can knock the screw-ends back and dress the surfaces. Usually I can just jig up these sorts of joints, but occasionally there is a truly stubborn or awkward one that I'll strap together first; old CLW second gen EMD nose castings, the three assemblies of a Kemtron geep body as examples. No reason this won't work for you unless Bob knows one, and the beauty is its all adjustable cold so not scary at all.
I agree the basic C-liner shell is a worthwhile subject, though one has to also watch the fan-count depending on the railroad modelled. Anyway, I'd think the best place to split that one would be just behind the cab doors.
I'd use three tabs sheared from thick brass strip as an alternative, one at the inside centre of the roof and one low on the inside of each side, drilled and tapped through some available flat area devoid of detail so they are easy to grind and blend afterwards.
Each screwed with brass 2-56 on both ends, you can loose them a little and adjust the relationships between the nose and the carbody until it's precisely where you want it. Doing the two sides first, up and down between the parts is a loosen-tighten deal, in and out a brass washer inserted under one or the other screw in a strip. Fore and aft is a loosen tighten deal too, but you have to decide if you want to fill the resulting gap or take it back apart and redress the joint (squaring on a piece of 3/8" plate glass with 320 wet-and-dry is a good way to go).
Once you have the two side strips tightened at your final alignment, then screw the strap in at the roof centre, adjust any tilt using the same methodology, and the whole is constrained/locked in place. Then you can crack out the torches and join the assembly.
Afterwards, you can knock the screw-ends back and dress the surfaces. Usually I can just jig up these sorts of joints, but occasionally there is a truly stubborn or awkward one that I'll strap together first; old CLW second gen EMD nose castings, the three assemblies of a Kemtron geep body as examples. No reason this won't work for you unless Bob knows one, and the beauty is its all adjustable cold so not scary at all.
No-one ever forgets where they buried the hatchet.
-
- Posts: 12858
- Joined: Sat Jan 13, 2007 7:57 pm
Re: Soldering Sand Cast Doorstops
That will work just fine. If you truly square the ends perfectly there is no reason your initial 2-56 holse would need adjustment. Just clamp, drill, tap, and assemble.
But truly squaring the ends means add the tabs later. Since I use my tabs for truck mount, they are too thick for good investment cast fidelity anyway.
I used the candle wax idea to create the B-17 windows on my first Erie-Built unit. You can use it to eradicate fans, change coupler pockets, etc.
But truly squaring the ends means add the tabs later. Since I use my tabs for truck mount, they are too thick for good investment cast fidelity anyway.
I used the candle wax idea to create the B-17 windows on my first Erie-Built unit. You can use it to eradicate fans, change coupler pockets, etc.
Re: Soldering Sand Cast Doorstops
Sarge, Bob,
Thanks for all the tips. I am leaning toward PRR. If not that NYC. It will likely be a bit until I scrape up the loot to get a casting done. I have to take a look at the PRR pilot (I have a couple of good photos). I might try and cobble one up with coupler doors. Definitely going with 4 wheel trucks. I always thought these were the best looking of the cab units. I think FM made a lot of good looking engines.
Rich
Thanks for all the tips. I am leaning toward PRR. If not that NYC. It will likely be a bit until I scrape up the loot to get a casting done. I have to take a look at the PRR pilot (I have a couple of good photos). I might try and cobble one up with coupler doors. Definitely going with 4 wheel trucks. I always thought these were the best looking of the cab units. I think FM made a lot of good looking engines.
Rich
Return to “O-Gauge, 2-Rail, Model Railroading”
Who is online
Users browsing this forum: No registered users and 25 guests